Nigeria's cement industry stands as a regional powerhouse. As of 2021, it had a combined capacity of 58.9 mt/y, making it the largest in Sub-Saharan Africa. Recent expansions by the leading cement manufacturers suggest capacity has increased, although it still lags behind the major cement producers globally.
An emerging oligopoly, it is led by three major operators: Dangote Cement, BUA Cement and Lafarge Africa, with market shares of 61.2%, 20.6% and 18.2%, respectively.
However, it faces a critical challenge: the persistently high cost of cement production and its far-reaching consequences for housing and infrastructure development across the nation. A February 2024 report noted that the price of cement in Nigeria had risen by 100% in three years due to soaring inflation, prompting calls for government intervention to rein it in. For any economy looking to scale infrastructure, inputs such as cement must be reasonably priced. Inflated prices can adversely affect development, leading to a bloated budget, substandard infrastructure, uncompleted and abandoned projects, a housing crisis, and skyrocketing rent. Examining how cement is made and its cost components is necessary to understand what drives the price of cement.
How cement is made
Dry-process cement manufacturing involves four main steps: extraction, crushing, clinkerisation, and grinding.
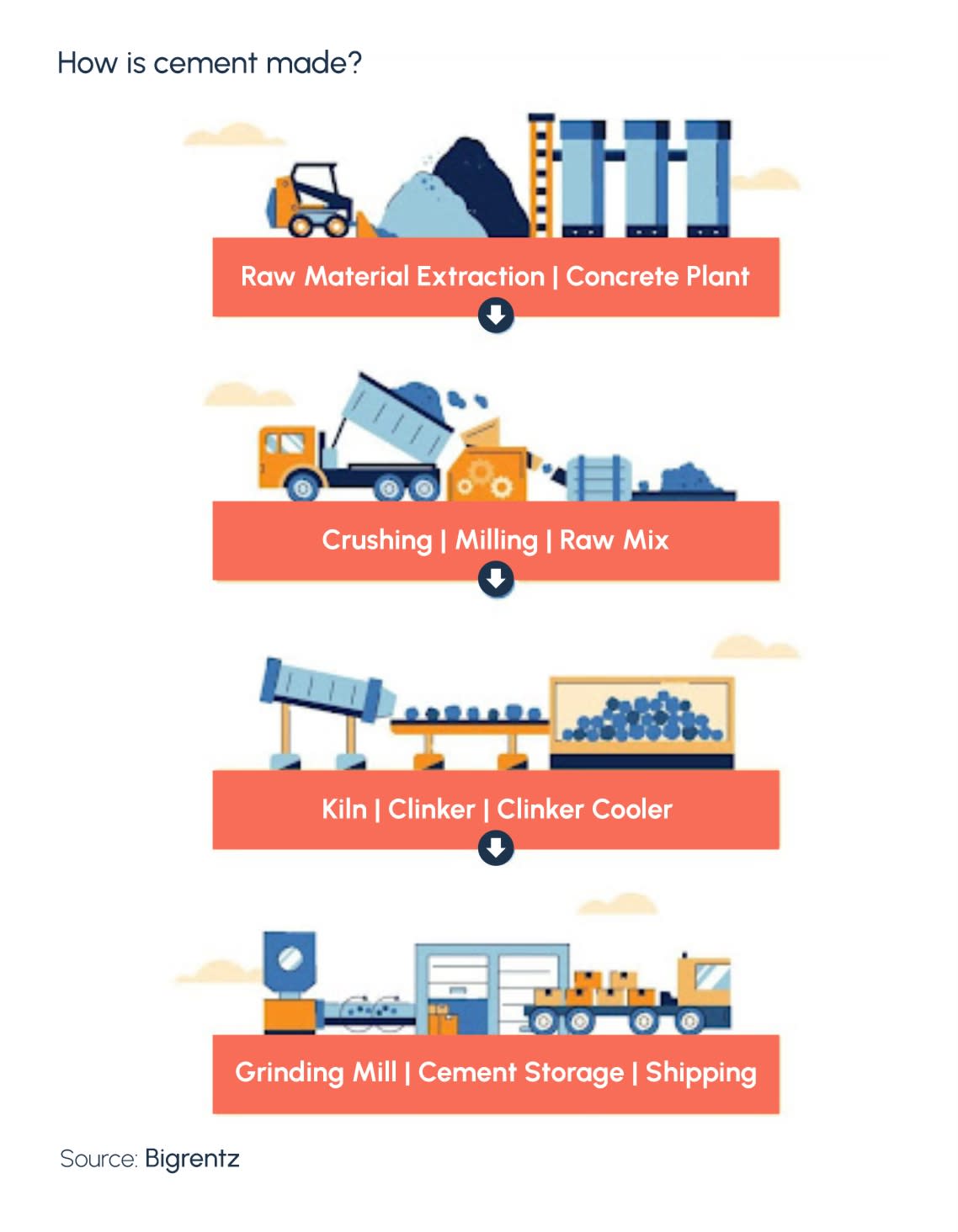
Raw materials such as clay and limestone come from quarries, with iron ore, and gypsum coming from mines where they are extracted. Limestone is the main ingredient, constituting about 62% of the total. The raw materials are crushed into gravel-sized components known as raw meal before moving to a mixing bay and then to the production facility.
Clinkerisation involves pyro-processing the raw meal in large kilns at temperatures as high as 1,450°C, resulting in an aggregate known as clinker. The clinker is then ground into a fine powder, and gypsum is added to control the cement setting.
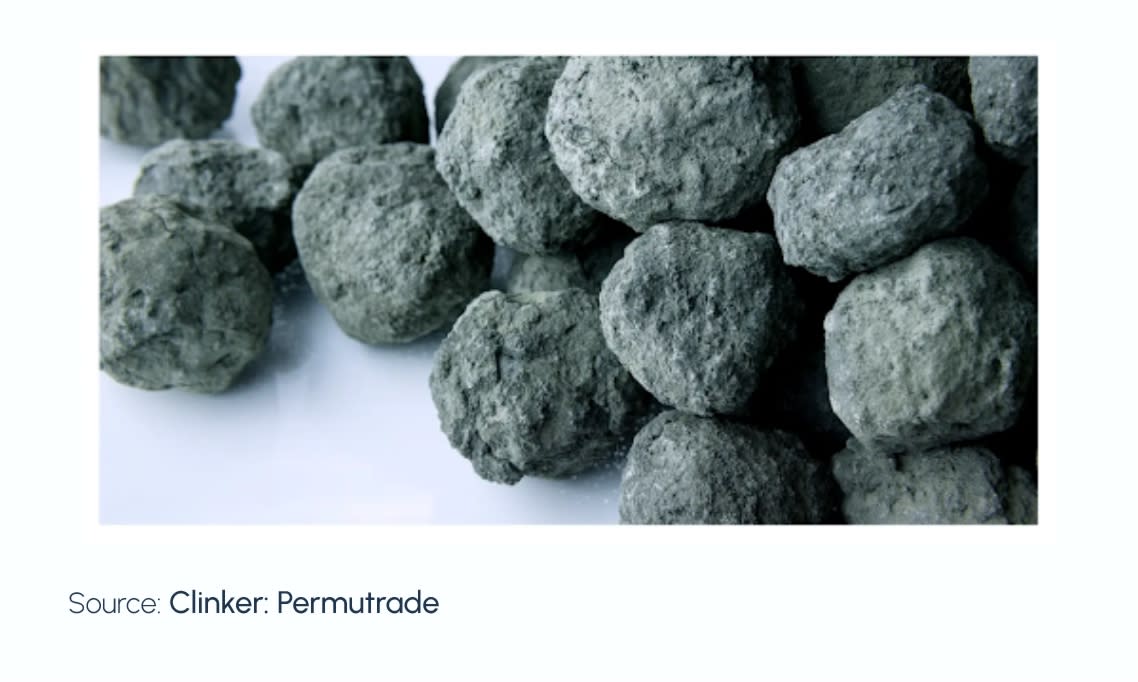
The product then undergoes quality control, packaging, and storage before being moved to warehousing depots.
Why Cement Is Expensive
Energy and logistics costs
Cement production is an energy-intensive process that is distributed as follows:
- 92.7% for pyro-processing during clinkerisation
- 5.4% for finishing grinding
- 1.9% for raw grinding
In Nigeria, producing a tonne of cement requires at least 105KwH of electricity, contributing to 40-50% of cement production costs. Due to insufficient national grid capacity, cement manufacturers must use natural gas to build their own power plants. Distribution costs also increase due to using diesel-powered trucks for transporting raw materials.
The unit fuel cost for cement production in Nigeria is estimated at $30 per tonne, which is costly compared to China—the world's biggest cement producer—at $6 per tonne. For context, in 2023, Dangote, Lafarge, and BUA spent ₦598.137 billion on fuel and power, a 42.45% increase from 2022.
Forex fluctuations and taxes
While recording a significant pre-tax profit in the first nine months of 2023, Dangote, BUA, and Lafarge Africa combined experienced forex losses averaging 441% year-on-year, amounting to ₦135.375 billion. Most of these losses are tied to sourcing natural gas denominated in dollars. Nigeria’s currency depreciation has led to a sustained rise in building materials costs, which are transferred to final consumers.
Additional costs arise from custom duties and taxes on imported materials, also indexed in dollars. According to the Federal Inland Revenue Service (FIRS), taxes from cement producers surpassed the combined taxes of all commercial banks in the country. In the past three years alone, Dangote Cement remitted ₦412.9 billion in taxes.
Seasonality
Cement prices vary with seasonal demand and are typically higher during the dry season than in the wet season. However, extraordinary circumstances can buck this trend.
Market dynamics
The cement industry has long operated a tacit arrangement driven by incentives. At one time, manufacturers were granted extensive tax holidays to encourage localised production, which led to a vibrant sector but raised concerns about protectionism and monopoly, keeping the industry anti-competitive.
BUA’s entrance into the cement market has led to the aggressive use of price wars to capture market share by reducing prices by as much as 36% in 2023. The tactic, combined with boosting its production capacity (+5.4% YoY volume growth in Q3 2023), has proved successful, as BUA’s market share grew by 9.4% to 20.6% in October 2023. Following calls for intervention earlier in the year, prices fell sharply from around ₦10,000-₦15,000 per bag to between ₦7000 to ₦8000 per bag on average, depending on location.
Impact on Housing and Development
Cement is the backbone of the housing and real estate sector, so it is vital that it continues to stimulate economic growth. While the latest data from the National Bureau of Statistics (NBS) show that it is one of the top ten contributors to GDP, an examination of the numbers points to a lull.
Real estate and construction accounted for 5.20% and 4.01% of economic activity in Q1 2024, a decrease from Q1 2023 (5.31% and 4.22%, respectively). In comparison, the housing sector in advanced economies like the United States contributes about 16% of GDP.
While cement's nominal contribution to GDP has risen, its share of GDP is falling:
According to the World Bank, the prices of intermediate inputs such as cement and steel reinforcement bars tend to be higher on average in Africa compared to other regions. This is important because higher prices for intermediate goods slow economic growth, which contradicts the general tendency for prices to rise with national income.
This presents a challenge for Nigeria, whose housing deficit is 15.56 million units and requires ₦21 trillion to address. With the prices of building materials accelerating and the economy unable to keep up, it becomes increasingly difficult to fund the national budget and bridge the housing and infrastructural gaps.
The Way Forward
To address the challenges posed by high cement costs, several practical steps can be taken:
- Implement energy-efficient technologies to reduce operational costs: Cement manufacturers can benefit from investing in research and development that explores diverse energy solutions and cheaper ways of production. There are plans in more advanced economies to adopt technologies such as carbon capturing, geopolymer concrete, cementless concrete, and concrete recycling to reduce carbon footprints and save energy.
- Improve transportation infrastructure: A revamped road and rail network would significantly reduce logistics costs, benefiting the cement industry and spilling over into other sectors of the economy. China’s famous Belt and Road Initiative has benefited immensely from its investment in transport infrastructure, making its cement industry a global leader.
- Review tax policies: To balance government revenue and industry growth, the government could consider revising duties for cement manufacturers who demonstrate a commitment to reducing costs and increasing affordability.
- Implement and enforce price monitoring mechanisms: It is not precisely clear how cement prices are arrived at as an established price mechanism appears not to exist, which explains anticompetitive conduct and price wars. Establishing a transparent system for monitoring cement prices will prevent price gouging nationwide. In India, for example, following reports of price collusion by a cement cartel, heavy fines were imposed to discourage the act. In the Philippines, the Department of Trade and Industry (DTI) regularly monitors and publishes suggested retail prices for cement to ensure fair pricing.
- Encourage sustainable building practices and local alternatives: Promoting alternative building materials and techniques like modular housing can reduce the reliance on cement. The supply can then be redirected towards infrastructural projects. Similarly, switching to locally-made materials can cut costs for manufacturers relying on imported raw materials. Pozzolana, used in Kenya and Turkey in place of imported clinker, lowers production costs in the cement-making process.
- Public-private partnerships for affordable housing: More collaborative projects between the government and private sector can help create large-scale affordable housing initiatives that benefit from economies of scale in cement procurement. However, for this to work, the government must be willing to offer incentives.
- Regional cooperation: Opportunities for regional cement trade agreements within West Africa in line with the AfCTA may help stabilise prices and ensure steady supply. This depends on how well the major manufacturers can ramp up supply, which still needs to grow to cater to the continent's infrastructural demand
Empirical evidence shows that no nation can progress if infrastructural burdens hamper it. A multipronged approach, such as the one mentioned, will drive development and resolve deficits to attain economic fulfilment.
References
Aditya, K. (2022, August). The cartelisation of the Indian cement industry. The Wire. https://thewire.in/business/the-cartelisation-of-the-indian-cement-industry-antitrust-report
Asoko Insights. (2023, June 7). Nigeria’s cement market. https://www.asokoinsight.com/content/market-insights/nigeria-cement-market
Cardinal Stone. (2024, January). Nigeria’s cement sector outlook. https://research.cardinalstone.com/storage/ResearchReports/Nigeria%20Cement%20Sector%20-%20Outlook%202024%20-%2008%20January%202024.pdf
China’s cement industry under the belt and road initiative. (n.d.). https://www.zkg.de/en/artikel/zkg_China_s_cement_industry_under_the_Belt_and_Road_Initiative-3535164.html
Uroko, C., & Onje, O. (2024, April 22). Cement: Retailers explain why prices are dropping. Business Day. https://businessday.ng/news/article/cement-retailers-explain-why-prices-are-dropping/
Peterside, D. (2024, February 6). The political economy of cement. Premium Times. https://www.premiumtimesng.com/opinion/671835-the-political-economy-of-cement-by-dakuku-peterside.html?tztc=1
Mbachu, D. (2023, November 16). Nigeria: Top cement producers battle for market share. The Africa Report. https://www.theafricareport.com/327057/nigeria-top-cement-producers-battle-for-market-share/
Encyclopedia MDPI. (2021). Cement production in Nigeria. Encyclopedia. https://encyclopedia.pub/entry/14248
National Bureau of Statistics. (n.d.). E-library. https://nigerianstat.gov.ng/elibrary/read/1241506
Fadayini, M., Madu, et al. (2021, May). Energy and economic comparison of different fuels in cement production. IntechOpen. https://www.intechopen.com/chapters/76509
Global Concrete Report. (2023). Scribd. https://www.scribd.com/document/624789246/Global-Concrete-Report-2023
Hundertmark, T., Reiter, S., & Schulze, P. (2021, December 16). Green growth avenues in the cement ecosystem. McKinsey & Company. https://www.mckinsey.com/industries/chemicals/our-insights/green-growth-avenues-in-the-cement-ecosystem
Aja, I. (2023). Nigeria cement producers endure forex losses. Nairametrics. https://nairametrics.com/2023/11/06/2023-9m-nigerian-cement-producers-endure-forex-losses-maintain-profits-amid-sector-decline/
Watts, J. (2019, February 25). Concrete: The most destructive material on Earth. The Guardian. https://www.theguardian.com/cities/2019/feb/25/concrete-the-most-destructive-material-on-earth
Ogundeji, J. (2024, February 11). Cement prices soar by 100% in three years. Punch. https://punchng.com/cement-price-soars-by-100-in-three-years/
Ogundeji, J. (2024, February 22). Housing firms, developers reject N8,000 cement price. Punch. https://punchng.com/housing-firms-developers-reject-n8000-cement-price/
Leone, A., Macchiavello, R., & Reed, T. (2021, June). The falling price of cement in Africa. World Bank. https://documents1.worldbank.org/curated/en/727041624328488778/pdf/The-Falling-Price-of-Cement-in-Africa.pdf
NESG. (2024, April). Bridging the housing and urban development divide. https://nesgroup.org/download_resource_documents/Bridging%20the%20Housing%20and%20Urban%20Development%20Divide._1713876197.pdf
State House. (2023, September). Nigeria needs N21tr to address housing deficit, says VP. https://statehouse.gov.ng/news/nigeria-needs-n21tr-toaddress-housing-deficit-says-vp-shettima/
US Bureau of Economic Analysis. (2024, March 28). GDP fourth quarter and year 2023 (third estimate). https://www.bea.gov/sites/default/files/2024-03/gdp4q23-3rd.pdf